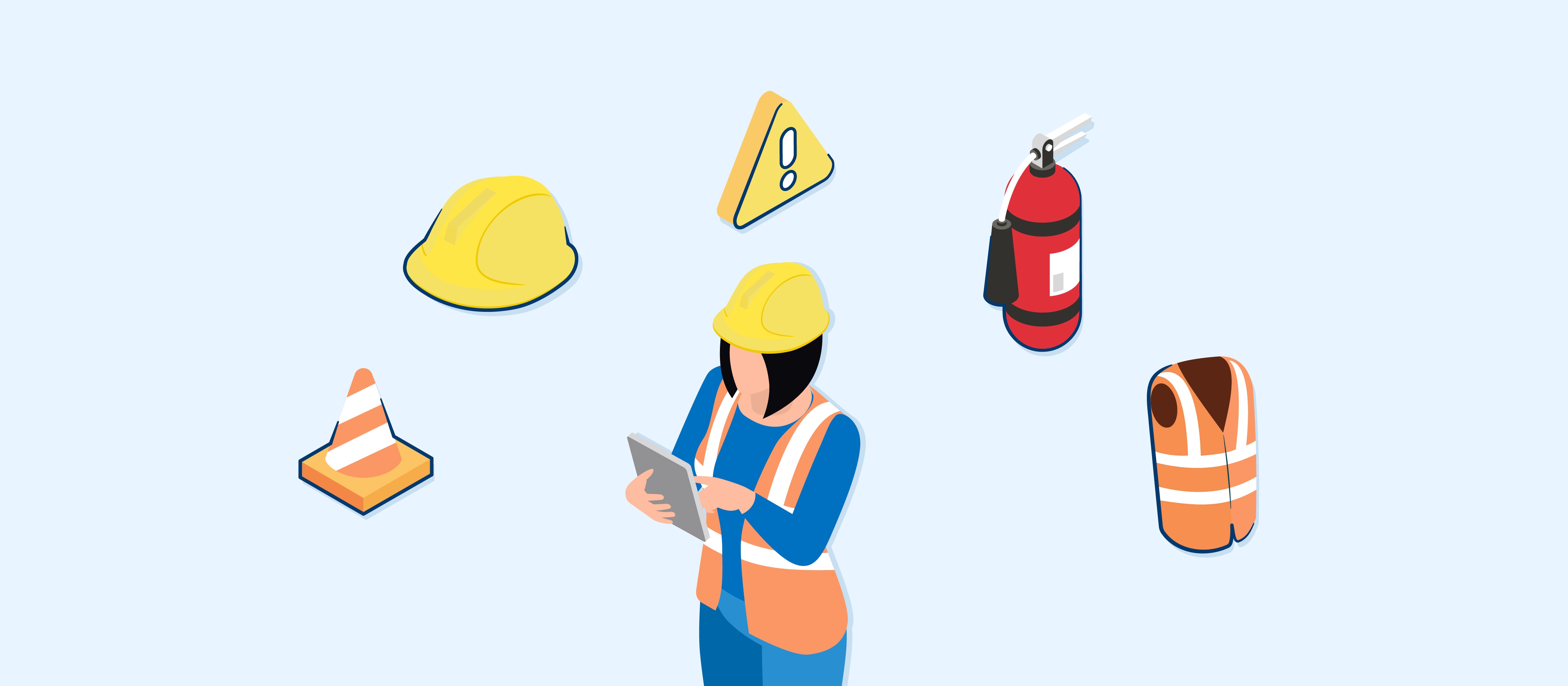
What is industrial hygiene and safety?
Any successful industrial business prioritizes operational efficiency and staff well-being. With this in mind, maintaining high standards of industrial hygiene and safety is crucial for protecting both your business’s profits and your people.
In the hustle and bustle of day to day operations, there are numerous hygiene and safety risks – whether it’s using complex machinery or dealing with sensitive chemicals and physical agents. That’s why we’re here to explore the common risks that industrial businesses face, the importance of reducing or eliminating them, and effective strategies to ensure a safe and healthy work environment.
What is the purpose of industrial hygiene and safety?
Industrial hygiene and safety, or occupational hygiene, is the process of anticipating, recognizing, evaluating, and controlling workplace hazards. [1] This means to ensure the health and well-being of your workers, which in turn, makes your business more efficient.
Why is industrial safety and hygiene important for your business?
Implementing industrial hygiene measures not only has several benefits for the people making your business possible but also for how much profit you make out of it.
Having a robust and strict occupational hygiene process can result in: [1]
Fewer workplace accidents
Preventing workplace accidents is essential to avoid serious injuries and health conditions among your staff. Less accidents also means your operation can run without interruptions.
Increased productivity and efficiency
A healthy workforce can result in fewer sick days, as well as increased motivation and quality of work.
Lower costs
Reducing staff absence and replacement due to illness can save you money. Increased hygiene and safety measures can also slash insurance costs and legal expenses. [4]
Reduced risk of occupational diseases
Minimal exposure to workplace hazards can decrease long-term and serious illnesses. These health risks can include respiratory conditions like asthma from smog inhalation, skin diseases due to chemical exposure, and even mesothelioma (cancer that develops in the lining of some organs) caused by asbestos exposure.
So, what exactly are workplace hazards and how can you prevent them? Let’s dive right into it.
What are industrial hygiene hazards?
In any industrial business, staff can encounter several hazards that could put their safety at risk. So, your industrial hygiene and safety programs should be designed to control all types of environmental health concerns.
According to the Occupational Safety and Health Administration (OSHA), a workplace or occupational hazard is: "any source of potential damage, harm or adverse health effects on something or someone under certain conditions at work”. [2]
These types of threats are typically broken down into categories, including: [3]
Biological hazards
Bacteria, viruses, and bodily fluids that can cause chronic infection or the spread of diseases such as foodborne illnesses and respiratory infections.
Physical hazards
These refer to agents such as excessive noise, unsafe working temperatures, and physical obstructions that can cause slips, trips, and falls.
Chemical hazards
This means hazardous chemicals that emit toxic fumes or vapors or are combustible/flammable.
Air contaminants
Basically, solid particles that travel in the air such as fibers and dust.
Ergonomic hazards
Tasks that involve repetitive and demanding movement over long periods of time can impact the body in many ways, making them ergonomic hazards. For example, injuries from operating heavy machinery or eye strain from poor lighting and excessive levels of vibration from loose tool parts.
How to avoid industrial hygiene hazards?
Every industrial business will have unique circumstances when it comes to exposure to hazards. However, some simple changes can go a long way in improving hygiene and keeping your employees safe.
Limit Biological Hazards
- Give workers easy access to hand sanitizer and hand soap to reduce the spread of bacteria and viruses.
- Train staff on proper hygiene procedures such as handwashing and personal hygiene.
- Implement a schedule for cleaning and disinfecting surfaces, especially in high-traffic areas.
- Monitor cuts and scrapes to limit exposure.
Prevent Physical Hazards
- Provide personal protective equipment - e.g. ear protection to reduce noise exposure.
- Place barriers between workers and hazardous equipment (known as engineering controls).
- Clearly mark safe walking pathways.
- Always keep pathways free of physical obstructions to prevent slips, trips, and falls.
Minimize Chemical Hazards
- Educate your employees on chemical hazard warning symbols.
- Store hazardous substances safely. This will usually be in a lockable cupboard situated below eye level (just make sure that incompatible chemicals are not stored in the same place).
- Provide personal protective equipment such as face masks or respirators. This will reduce the risk of breathing in or having direct contact with toxic chemicals, fumes, or vapors.
Limit Air Contamination
Providing face masks and respirators can also reduce the risk of exposure to dust and other fibers in the air, improving indoor air quality. Aside from this, you can also:
- Store loose and raw materials either indoors or in sealed containers.
- Invest in oxidizers (a special heating unit) to destroy pollutants before they can get into the air.
- Ensure proper ventilation and reduce solvent and CFC levels, especially in confined spaces. One way to help decrease the amount of chemicals used is to use wipers instead of solvents to reduce CFC fumes in the air.
Avoid Ergonomic Hazards
- Train all staff on manual handling to encourage safe heavy lifting methods.
- Keep operational equipment within easy reach and automatize constant tasks to prevent issues like repetitive strain injuries and carpal tunnel syndrome.
- Provide padding for tools to reduce the risk of contact with sharp, hard, or vibrating surfaces.
With so many types of hazards to think of and even more ways to prevent them, getting the right guidance and expertise will ensure the highest levels of hygiene and safety in your facility.
Who is responsible for industrial hygiene in the workplace?
Hygiene and safety in the workplace are everyone's responsibility. However, it is the job of an industrial hygienist to create an efficient process to ensure that potential hazards are avoided.
What does an industrial hygienist do?
Industrial hygienists (also known as environmental hygienists or occupational hygienists) are responsible for assessing the potential risks and hazards in a workplace through both practical and analytical methods. They create and implement strategies to mitigate or eliminate the risk to worker's safety and well-being. This is carried out through a process known as Industrial Hygiene Monitoring, Environmental Monitoring, or IH Monitoring.
The key components of the industrial hygiene profession are:
- Implementing administrative controls like training staff about occupational health, hygiene, and safety.
- Researching the effects of exposure to various hazardous materials on human health.
- Carrying out risk assessments to find out the extent of worker exposure. This could involve taking samples (IH sampling or Industrial Hygiene Sampling) or checking the use of heavy machinery for comfort and excessive exertion.
- Creating industrial hygiene programs and recommending ways to control or eliminate hazards. This is known as an Industrial Hygiene Monitoring Plan (IHMP).
What could be included in an Industrial Hygiene Monitoring Plan?
Once an industrial hygienist has assessed a workplace, they will develop an Industrial Hygiene Monitoring Plan. By completing this task, an industrial hygienist can make sure that your facility operates not only efficiently but safely too. This plan protects your employees by following a few steps:
1. Hazard Anticipation
Hazard anticipation involves assessing a facility based on numerous factors (nature of the work, exposure to chemicals, workplace population, among others) and identifying the potential for damage to occur.
An example of hazard anticipation is the use of Safety Data Sheets (SDS). These sheets are created by manufacturers and contain all of the properties of each chemical that staff can potentially come into contact with.
OSHA's Permissible Exposure Limits (PELs) lists the acceptable level and duration of exposure for each substance. [5] This is also sometimes known as Occupational Exposure Limits.
2. Hazard Recognition
Once hazards have been anticipated, the industrial hygienist will identify the factors in your establishment that may cause them. For instance, they may identify a lack of ventilation in a manufacturing facility that is prone to dust.
3. Hazard Evaluation
The hygienist will then evaluate if the potentially hazardous conditions are creating safety issues and compare these conditions against occupational hygiene regulations and exposure standards. This could involve evaluating hazardous sound exposure or lack of ventilation, for example.
In the case of ergonomic hazards, the hygienist may observe workers as they carry out their duties and even ask how at risk they feel they are.
4. Hazard Control
The final step of the plan will be to implement measures that control and prevent each type of hazard from occurring. The industrial hygienist will first assess how essential to your business it is to expose staff to these hazards, then analyze them, and finally, recommend which ones to remove.
If some hazards cannot be eliminated, the hygienist will make recommendations and enforce safety protocols to reduce exposure to them.
Industrial settings with safe and healthy workplace conditions offer a wide range of benefits to not only employees but also your business's efficiency and profits. Consulting an occupational hygienist and creating an extensive and efficient IHMP, along with staff following controls, ensures that your facility will be a safe and hygienic place for all.
Hygiene and safety in an industrial setting is everyone’s responsibility. To keep staff up to date on effective hand hygiene procedures, find out more about correct handwashing techniques and how to implement them. Or if you're looking for ways to improve your facility beyond hygiene and safety, why not learn more about how Tork Vision Cleaning management software can maximize efficiency?
Reference:
[1] Occupational Safety and Health Administration. (n.d.). Industrial hygiene. U.S. Department of Labor.
[2] Occupational Safety and Health Administration. (n.d.). Job hazard analysis and job safety analysis: Training manual. U.S. Department of Labor.
[4] British Safety Council. (n.d.). The business benefits: Health and safety literature review.